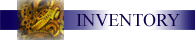
Working with Inventory
Before starting, insure that your Systems Administrator has CONFIGURED your
privileges to allow you all of the features you will need from the INVENTORY
Module.
On this page you will find the following items:
An explanation
of the inventory system
Getting Started with INVENTORY
RECEIVE
INVENTORY
RECONCILE
INVENTORY
TRANSFER INVENTORY
The ability to attach inventory
from the inventory system to channel records and eWorkRequests is now available.
As with other features, this one must be enabled in the channel configuration to
be available to records in the channel. When enabled, each record in the
channel displays an INVENTORY link, next to the MEMBERS link (if used) and the
record number/name in the green bar. Clicking on the inventory link takes
you to the record's inventory screen, from which all inventory for the record is
managed.
Use of this screen begins by searching for an inventory item. This is done
by filling in a partial item number or name in the search box and clicking the
search button. The search results are displayed in a pick-list from which
an item may be selected. If the desired item isn't found, the search may be
repeated. Once the desired item is displayed, the user chooses the
appropriate item, specifies a quantity (which must be less than or equal to the
total quantity available in the system) and clicks the RESERVE button.
This creates an inventory record in the channel record, and reserves the
appropriate quantity of that item both in the channel record and in the
inventory system. The available quantity is reduced by the reserved
quantity. It is not possible to reserve more items than are actually on hand in
the system.
Each inventory item in the channel record is displayed in the next section of
the screen, showing the total reserved, total issued to the channel record, and
providing some controls to allow for the update of the inventory in the record.
By entering a quantity and clicking RELEASE, the user can cancel all or part of
the inventory reserved. The revised reservation is applied to the channel
record and the system-wide inventory record. If the user releases ALL the
inventory, the item is deleted from the channel record. It is not possible
to increase a reservation - the reservation must be cancelled first (by
releasing the entire quantity) and then a new reservation placed with a higher
quantity if desired.
When the worker goes to the warehouse to pickup the item, the item is physically
transferred to the channel record. This is done by entering a quantity and
a warehouse, and clicking ISSUE (The user must have inventory adjust privileges
to do this, or to return inventory - see below.) Issuing inventory
removes it from the amount on hand in the warehouse and system-wide, and also
removes the reserved amount, adjusting all the records appropriately. For
example, if you have 100 items on hand, 50 of which are reserved, leaving 50
available, and you issue 25 of those from a warehouse to the channel record, the
channel record will now show 25 reserved and 25 issued, and the inventory item
record will now show 75 on hand, 25 reserved, and (still) 50 available.
It is possible to issue MORE items than were reserved. In this case, the
items are issued, the reserved amount is reduced to zero, and all records are
updated appropriately. However, it is not possible to issue more items
from a warehouse than the warehouse has on hand.
In the event that more items are needed later, more items can be issued from the
same or a different warehouse. Again, all numbers are adjusted appropriately.
In the event that a technician does not use all the items he or she was issued,
the technician can return the items to a warehouse. At that point,
the user would enter the number returned, indicate which warehouse was receiving
the returned goods, and click RETURN. As with everything else, the
numbers will be adjusted appropriately. The act of returning items
does NOT affect items reserved. If 50 items were initially reserved, and
25 were issued, leaving 25 reserved, and the user returns the 25 items, the
record will now show 25 reserved, and zero issued. If the user no longer
wishes to hold the 25 remaining reserved items, they should release the 25
reserved items.
If the user returns ALL the inventory items that were issued, and no more are
reserved, the inventory item record is deleted from the channel record.
The Inventory section of the
program is where all of your work is accomplished for creating,
modifying, and tracking of your inventory. We start by creating items to
be inventoried. Next we create a location for the inventoried items to be
stored. Then we create inventory location; and track, or transfer items
from one inventory location to another.
RECEIVE INVENTORY
A new Receive system allows for inventory to be received at a warehouse en
masse. The user specifies which warehouse they are receiving at, and
they are then presented with a screen on which they may indicate quantities of
items received. Optionally, the user may display only the inventory items from a
specific vendor (when the vendor module is licensed), to more easily enable the
receipt of vendor orders.
RECONCILE INVENTORY
A new Reconcile system allows for easy warehouse inventory reconciliation.
The user is presented with a form, which may be printed and used to reconcile
warehouse inventory. Once the paper form is completed, any corrected
quantities can be entered on screen and updated all at once.
TRANSFER INVENTORY
This screen allows for the transfer of inventory items from one warehouse to
another. The transfer is initiated as the user specifies the
quantities of items to be transferred. Once the quantities are
entered and verified, a transfer ticket is displayed, and may be printed and
sent with the transferred inventory. When the inventory arrives at
the destination warehouse, the operator may display an electronic copy of the
ticket, and receive all the items on the ticket with one click.
These three systems are all very simple and similar, being based on the same
program code. They use a step-by-step method to walk the operator
through a four-phase system to perform the desired operations.
|